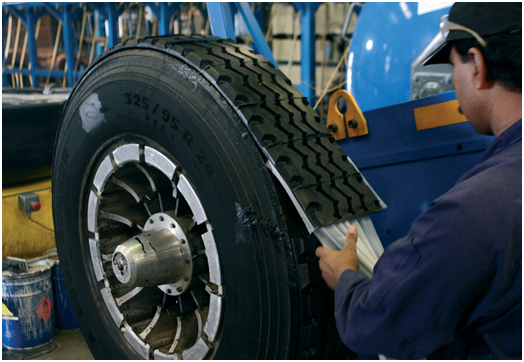
Tire recycling, also known as rubber recycling, refers to the process of recycling used vehicle tires that can no longer be used on the vehicles due to wear and tear or irreparable damage. Used tires are among the most problematic and challenging sources of solid waste. This is due to their large volume, their resilience, and the fact that they contain components that pose a threat to the environment and to the people around. They also become the home ground for mosquitoes and rodents which are responsible for carrying many diseases.
It is estimated that over 250,000,000 tires are thrown away annually. Because of this high availability, resilience, bulk and non-biodegradability, tires are prime targets for recycling.
Process of Tire Recycling
- Collection of Used or Worn Out Tires
In every recycling process, collection is usually the first step. Here, tires are collected by individuals and some business individuals who have ventured into tire recycling business. People are paid for collecting tires and sending them to collection points. Once the tires reach the required number or volume, they are packed in huge tracks and sent to the processing plants for processing. Although it is considered a profitable venture, some people prefer reusing these used tires for other purposes at home. A good example is using the tires as rubber mulch, used in jungle gyms for strength, speed agility and resilience training.
- Whole Tire Processing
At the processing plant, processing basically starts with cutting the tires into tiny pieces. This is an important step that aims to reduce the volume of the tires and create a material that can be handled easily. The tire shredders (the machines specially designed to shred tires) basically shred or cut tires using two counter rotating shafts which produces 2 inch pieces. The end product of this stage can be used as a raw material for tire derived fuel. Tire processing employs one of these two systems:
- Mechanical systems
The mechanical systems grind scrap tires into small chips using the ambient process. In a typical ambient system, the rubber shreds are put into one granulator fitted with screens that help in determination of the product size.
- Cryogenic systems
These systems freeze tires at very low temperatures. This shutters the rubber to create different chip sizes. The tire shreds are then supper cooled using liquid nitrogen. The extremely brittle, cold rubber is then passed through a hammer mill which shatters the rubber into very tiny particles. From these tiny particles, steel is removed using powerful magnets and fibers are separated with air classifiers. Finally, clean recycled rubber is obtained and can used in other applications.
- Steel Liberation Stage
The tire shreds obtained from step 1 are processed and prepared for the elimination and separation of the tire wire from the rubber. This important step includes fiber separation and course screening. Tires contain steel wires for resilience, strength and versatility. The steel wires are removed, recycled and sent to steel rolling mills for the manufacture of new steel. The remaining rubber can be sold as rubber mulch or can be used as playground or field turf or used as crumb rubber feed stock.
- Screening and Milling Stage
Once the wires are separated from the rubber, the next stage is screening. This involves careful observation of the rubber to ensure there are no more wires or other contaminations. The screening process is all about screening a huge number of different sized rubbers which contain no wires, sorting them into varied sizes, eliminating all unwanted substances, and the reduction of extra-large and unwanted rubber pieces.
- Cleaning Stage
Once the screening process is complete, the next step is the cleaning stage. Here, the rubber obtained from the screening and milling stage is thoroughly cleaned. This process involves the use of water and other cleaning agents to thoroughly clean the rubber. Once the clean rubber is obtained, it can be packed and transported to other factories that require rubber as a raw material in their processing plants. For example, rubber shoes manufacturers, playground turf manufacturers and other rubber applications.